Envision the benefits of owning your own private airfield, offering the freedom to take flight at your convenience, without the hassle of traffic, security protocols, or delays. What if you could design and personalize this exclusive airstrip to align with your unique preferences and needs?
Whether you are a private developer or an individual looking to implement a grass strip or paved runway, considering a simple or sophisticated design, there are several key factors to consider before getting started. Planning, designing, and implementing a private airfield requires careful analysis of site selection, adherence to federal, state, and local regulations, safety measures, environmental impact, costs, maintenance protocols, and future needs. In this article, we discuss 10 important considerations to keep in mind to help your private runway dream take flight.
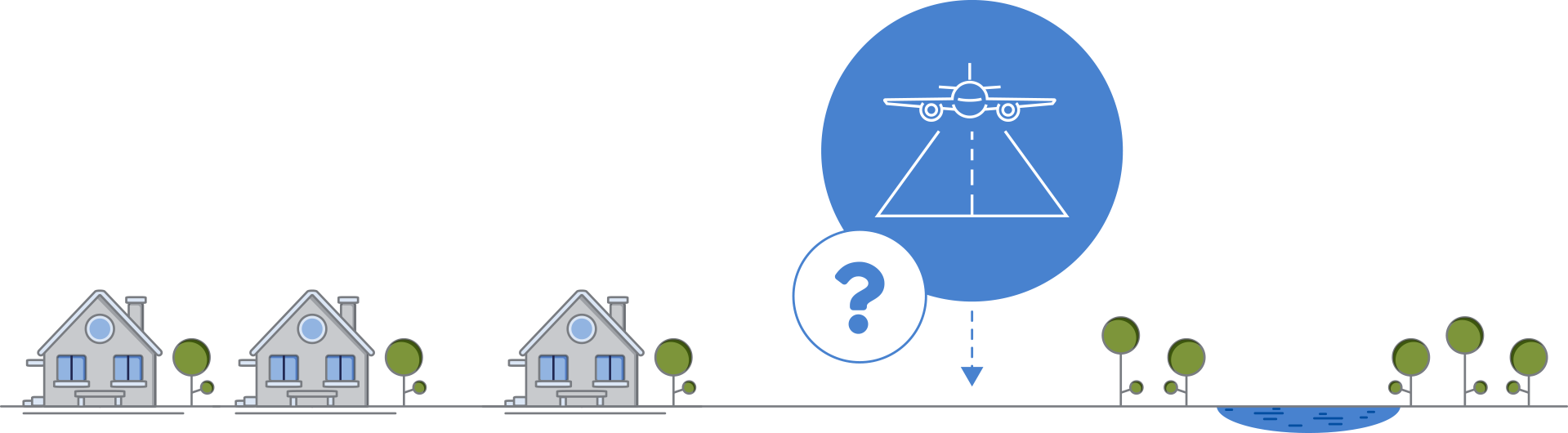
“For our clients, having their own backyard runway is perhaps the ultimate in privacy and convenience, and is more achievable than most would anticipate.”
– Matt Stewart, airport planner and project manager
1. Start with a strategic needs assessment and siting analysis
Your first step is to evaluate the size of the runway based on what types of aircraft you currently operate, or the type of aircraft you could potentially operate in the future, as runway pavements can last well over 20 years without reconstruction. Conducting a comprehensive evaluation of current and future aircraft needs, projecting requirements for the next two decades, and completing an in-depth analysis of your property will help identify where a private airfield could potentially be constructed. This involves several important considerations such as runway size, orientation, wind coverage, and required materials, with a focus on accommodating your personal aircraft, from single-engine planes to private jets. This assessment will also help guide the choice between a grass strip or a paved runway based on operational demands./p>
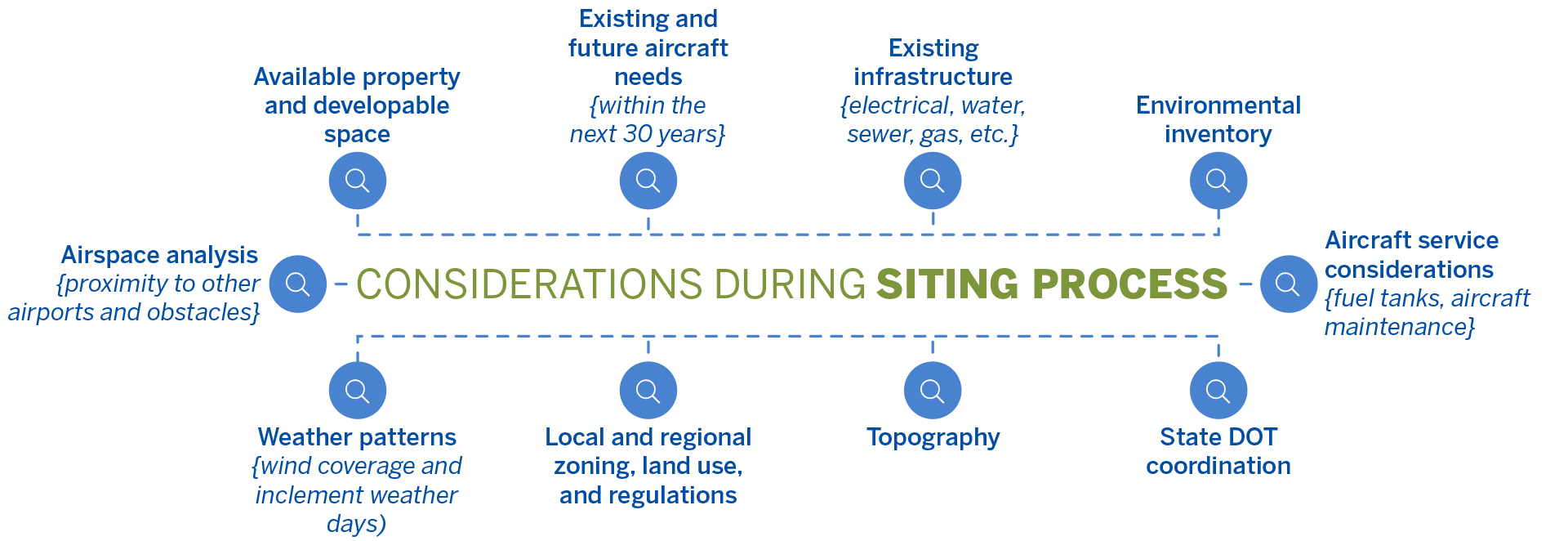
Siting the runway in a way that will extend the longevity and usability of the airfield is an important step to make sure you have the necessary space required. You’ll want to conduct an exhaustive analysis of the terrain, length required, and location in order to strategically position the runway for functionality. This initial on-site visit is a critical early step to address safety and permitting concerns, making necessary adjustments based on site analysis findings.
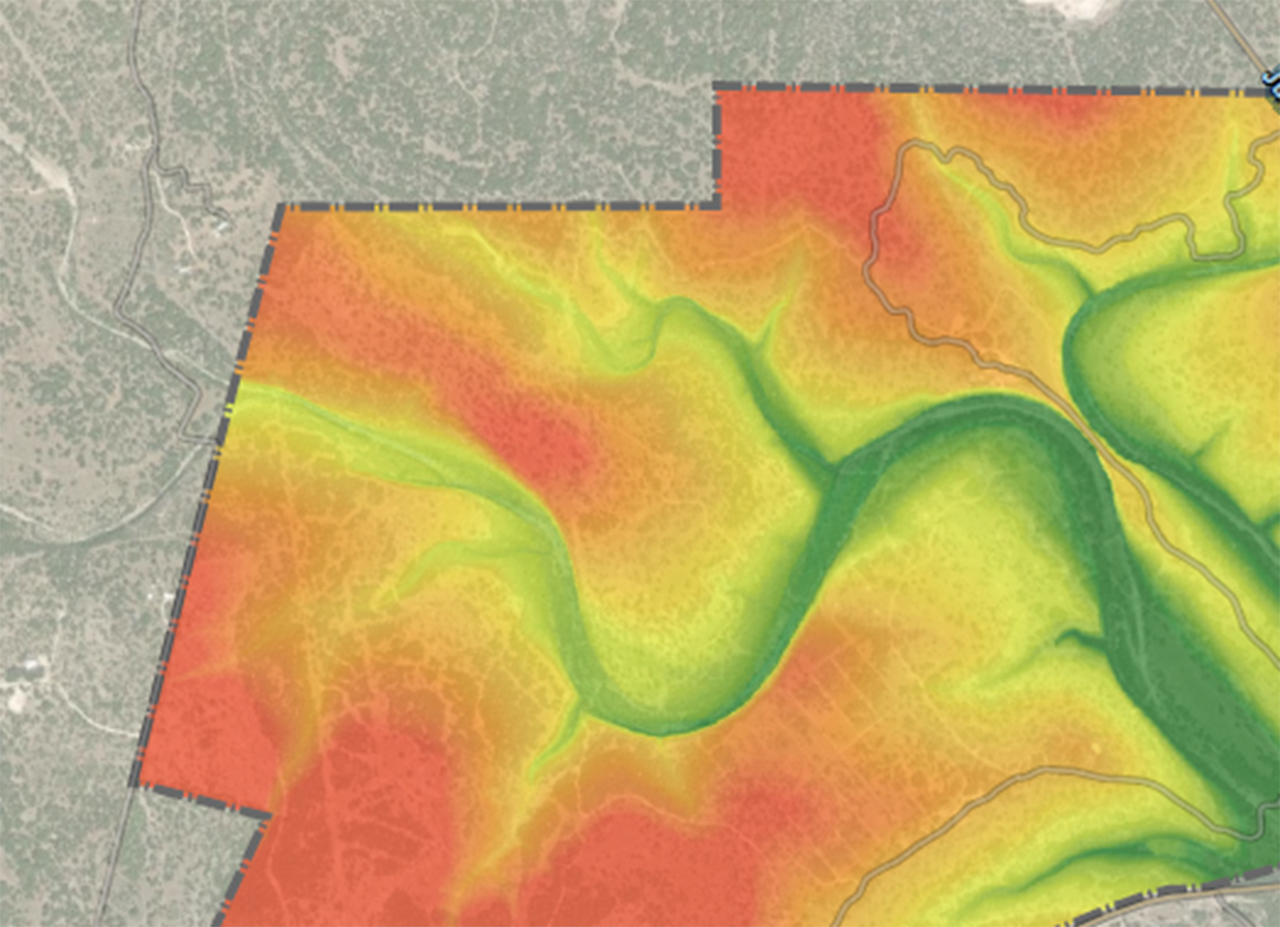
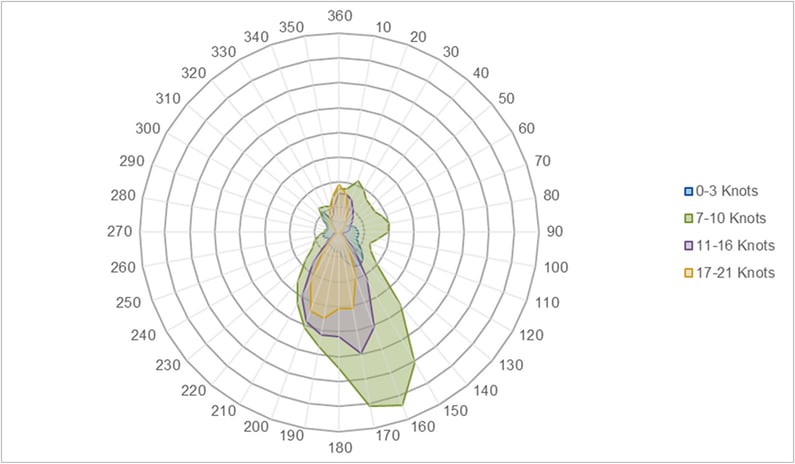
2. Prepare your budget, strategically
You’ll want to develop a comprehensive and detailed budget plan that covers design, construction, and ongoing maintenance costs. Explore potential funding sources or grants available for private runway owners and be sure to adjust the budget as needed based on ongoing assessments and changes in project scope. Having up-to-date cost estimates for equipment, lighting, and pavement materials is essential in ensuring the success and efficiency of your project during design and construction. Accurate cost estimates provide stakeholders with the necessary financial insights to plan, budget, and allocate resources effectively.
When it comes to equipment and materials, knowing the current market prices for fixtures, systems, and tools helps avoid cost overruns and ensures that the right equipment is acquired for the job. Up-to-date lighting cost estimates enable the selection of energy-efficient and cost-effective solutions, which can lead to long-term savings. Moreover, having accurate estimates for available pavement materials ensures that projects are not only completed on time but also with materials that meet quality standards. Keeping these estimates current helps to avoid unexpected expenses and delays, ultimately contributing to the overall success of your airport.
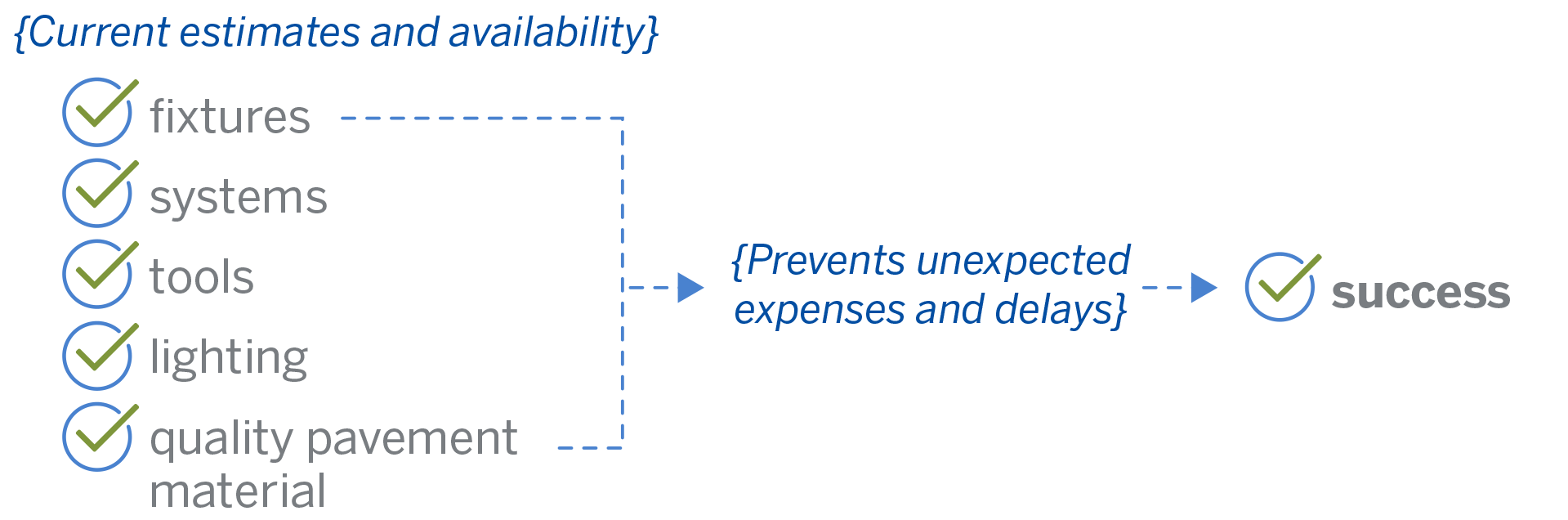
3. Create a realistic schedule
Schedule is as important as cost, and they go hand in hand because each affects the other. Creating and managing a realistic, aggressive schedule can mean the difference in a successful project or a completely frustrating one. Having the right team that can identify specific critical paths and milestones and integrating those into the plan is both a science and an art. Understanding a client’s schedule and aligning that with design and construction is the role of the team, and prevents unnecessary delays while ensuring a smooth project from concept through completion.
“We all have one common goal, whether you are the engineer, program manager, or contractor, and that is to deliver the project on time, on budget, with no surprises.”
– Randy Jenniges, SEH director of land development
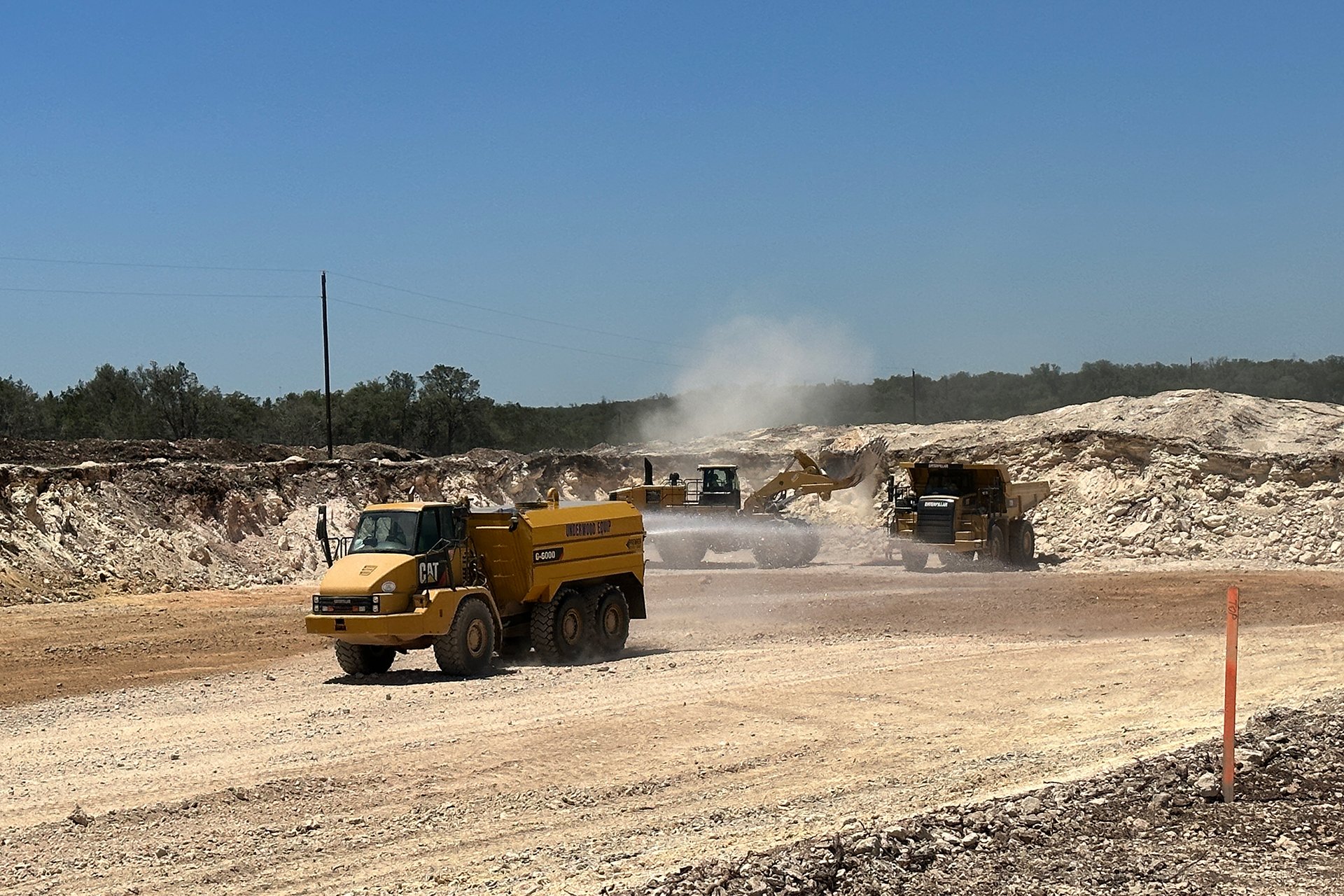
4. Navigate regulatory compliance
Your design team will need to carefully research local zoning and land use regulations that apply to your property, as well as any state regulations governing such construction. Obtaining permits or approvals from the relevant state, county, or city authorities may be necessary before you can proceed. It is also crucial to collaborate with the FAA, incorporating their recommendations and addressing any concerns or prohibitions they may have.
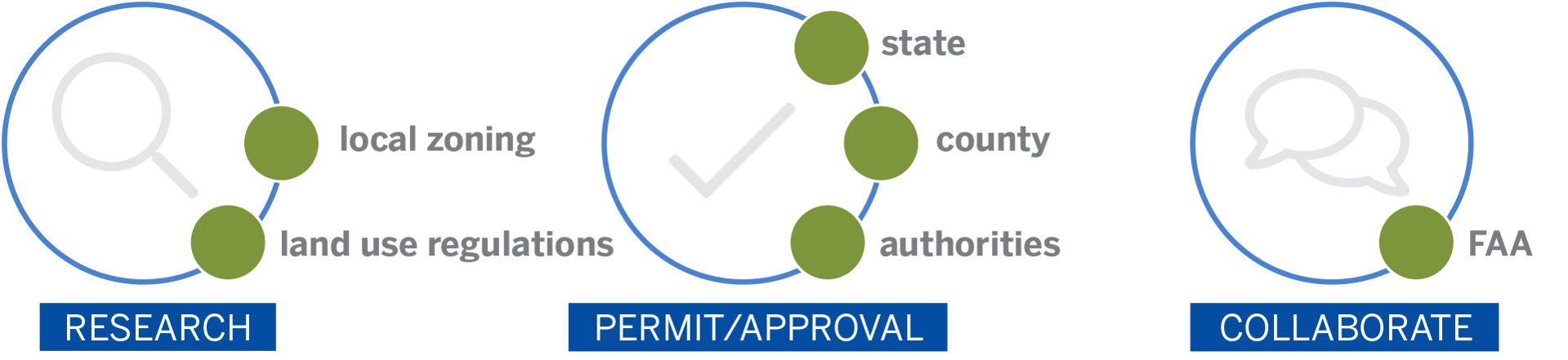
Throughout the entire construction process, strict adherence to regulatory standards is essential. For example, private airfield owners are required to submit a Landing Area Proposal (LAP) to the Federal Aviation Administration (FAA) at least 90 days before beginning construction by filing an FAA Form 7480-1. The 7480-1 is a document used to notify the FAA of any construction, alteration, activation, deactivation, or change to the status or use of a civil or joint-use (civil/military) airport. The form is required under Title 14 Code of Federal Regulations Part 157 and aims to ensure the safety and efficiency of the National Airspace System. While this might seem daunting, an aviation-focused engineer and planner can help successfully navigate this review process.
5. Optimize for efficiency and functionality
During design, it is important to consider factors such as the location of taxiways and apron space. This step helps to create a streamlined and efficient runway system. While most private airfields don’t construct a taxiway network seen at other airports, identifying the needs of the users early in the project will help determine what type of pavement infrastructure will be needed to support the operations.
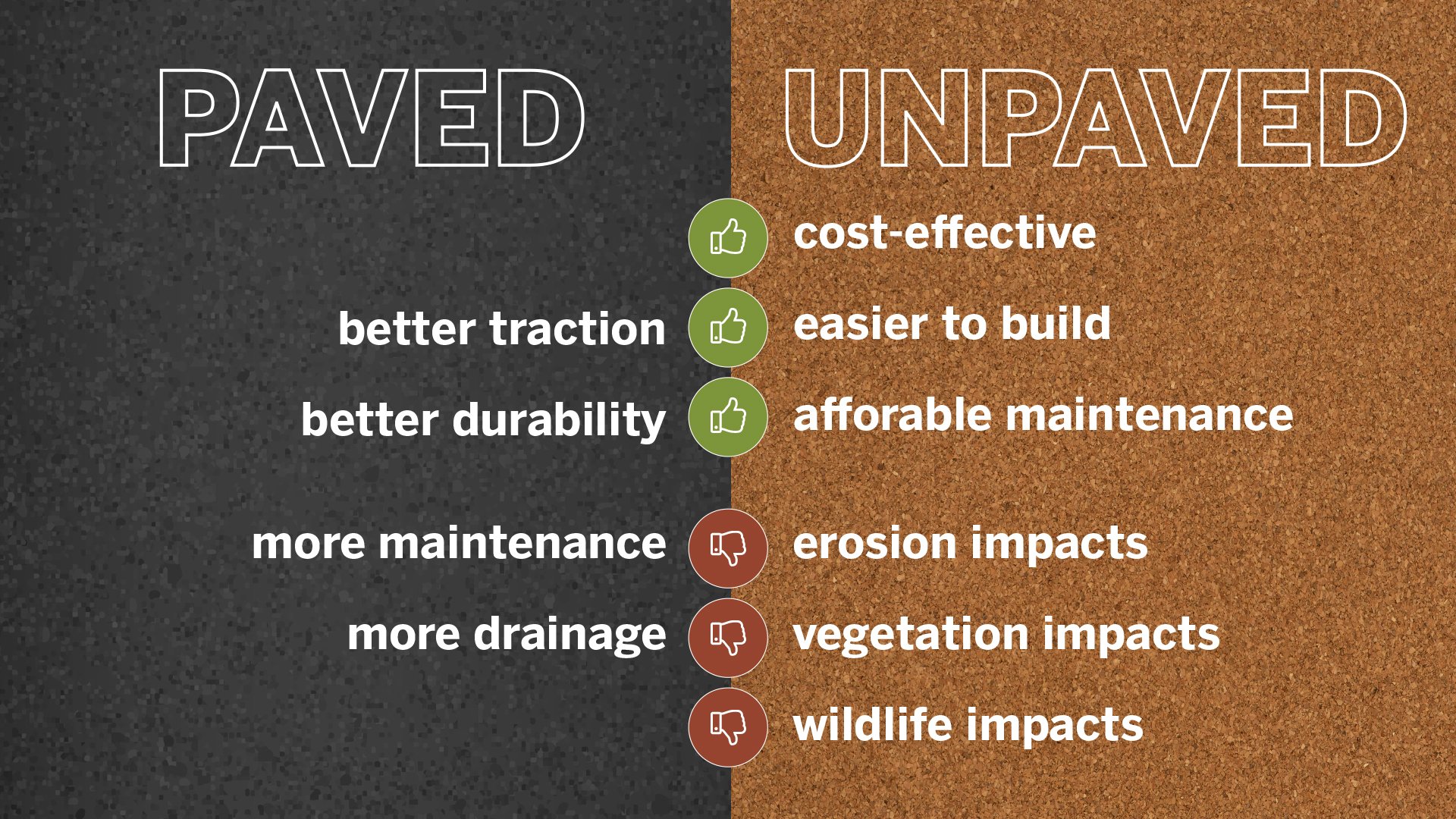
The surface of your runway can be either paved or unpaved, depending on your preference and budget. A paved runway may require more maintenance and drainage but can provide better traction and durability. An unpaved runway may be more cost-effective, easier to build, and provide affordable maintenance, but can be impacted by erosion, vegetation, or wildlife.
When you are ready to finally dig in, you’ll need to clear and level the land according to aviation design standards, ensuring the installation of necessary infrastructure such as lighting, signage, and safety features. This step is crucial to create a well-prepared foundation for the runway's construction and operation.
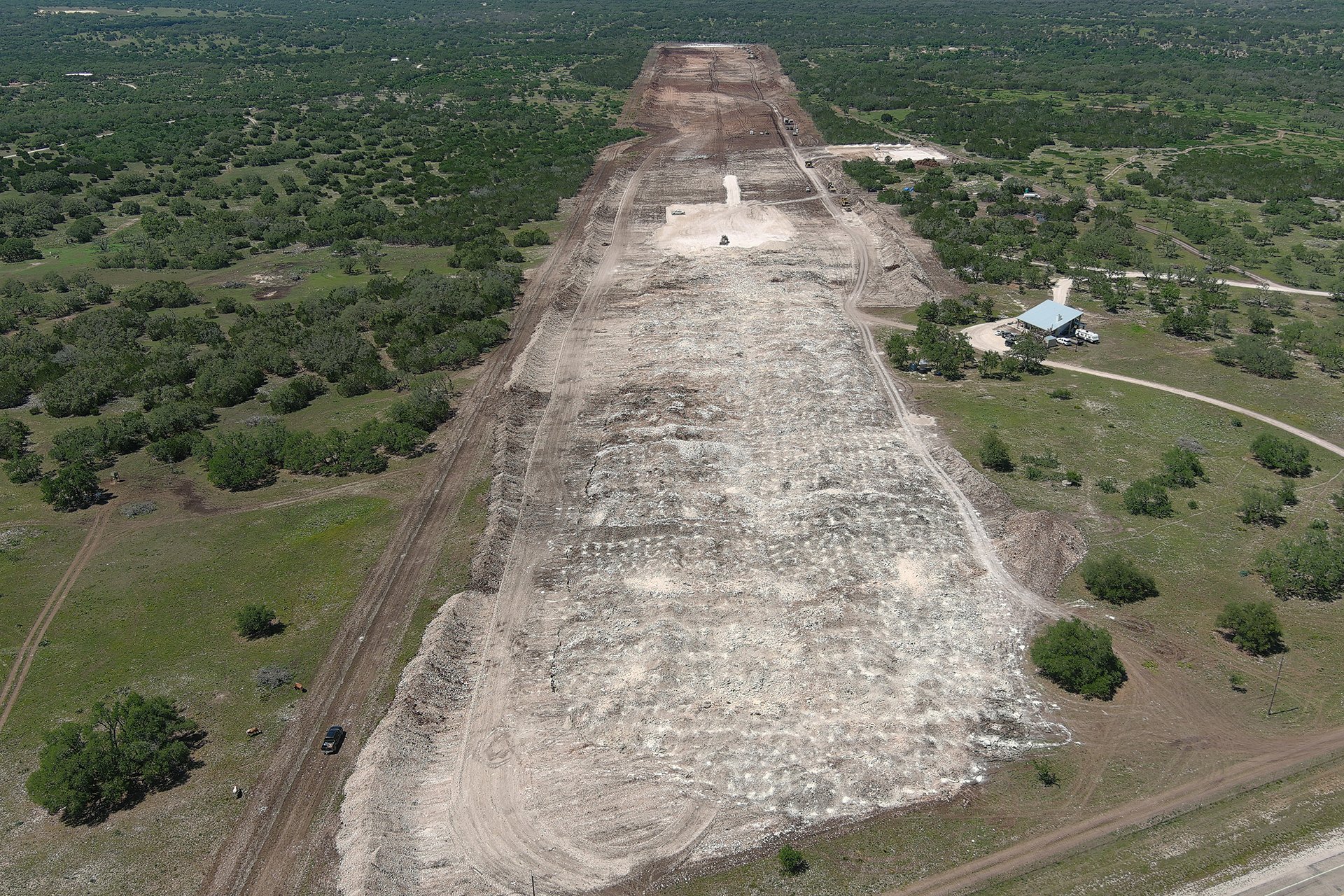
6. Engage a program manager for seamless execution
You are busy. The benefits of having a private runway on your property are to save time and provide convenience for you and your family. So, when it comes time to build your dream, why not take the same approach? Having a program manager on your team allows you to continue your everyday activity and have a one-stop shop. They can provide the correct oversight to align with your objectives that minimize delays, cost overruns, and potential conflicts.
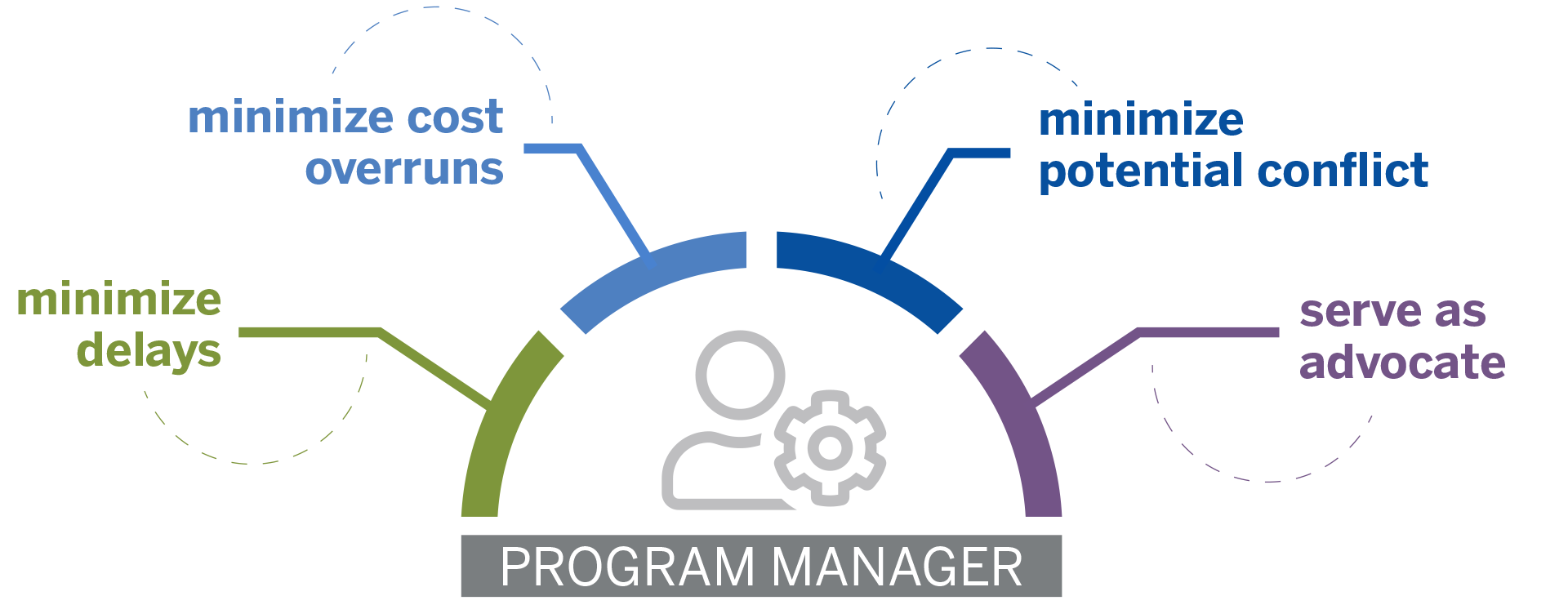
A program manager's role extends beyond project oversight; they serve as your advocate, ensuring they tailor strategies to your specific needs and site conditions. This proactive approach not only fosters efficiency but also cultivates trust and transparency throughout the project lifecycle.
“Being at the table with the client and engineer early at the start of the project allows the opportunity to fully understand the clients’ needs, parameters, and site conditions/constraints. This in turn drives the focus and effort on design, budgeting, and schedule. On a recent project, we partnered with SEH early on a 5,400’ design-build private runway in challenging terrain. The results were delivered in advance of schedule by four months, under-running the initial budget by more than 5%, and an extremely satisfied client. The more time the contractor can be engaged on the front end, the greater the likelihood of uncovering opportunities for creating value.”
– Kyle Moore, managing director, Koho Development
7. Partner with a contractor early
Partnering with a quality contractor early in the process allows the owner to benefit from the experience of the contractor from start to finish to make informed decisions, optimize resources, and mitigate risk from the onset. A seasoned contractor brings a wealth of experience spanning cost history, feasibility, construction methodologies, material insights, and subcontractor input. It can also help foster synergy among all stakeholders. From fine-tuning construction methods to aligning with aggressive schedules, their input ensures that every phase of the project progresses seamlessly. By leveraging their expertise early in the process, you can not only expedite the construction operation but also elevate the overall quality and longevity of your private airfield.
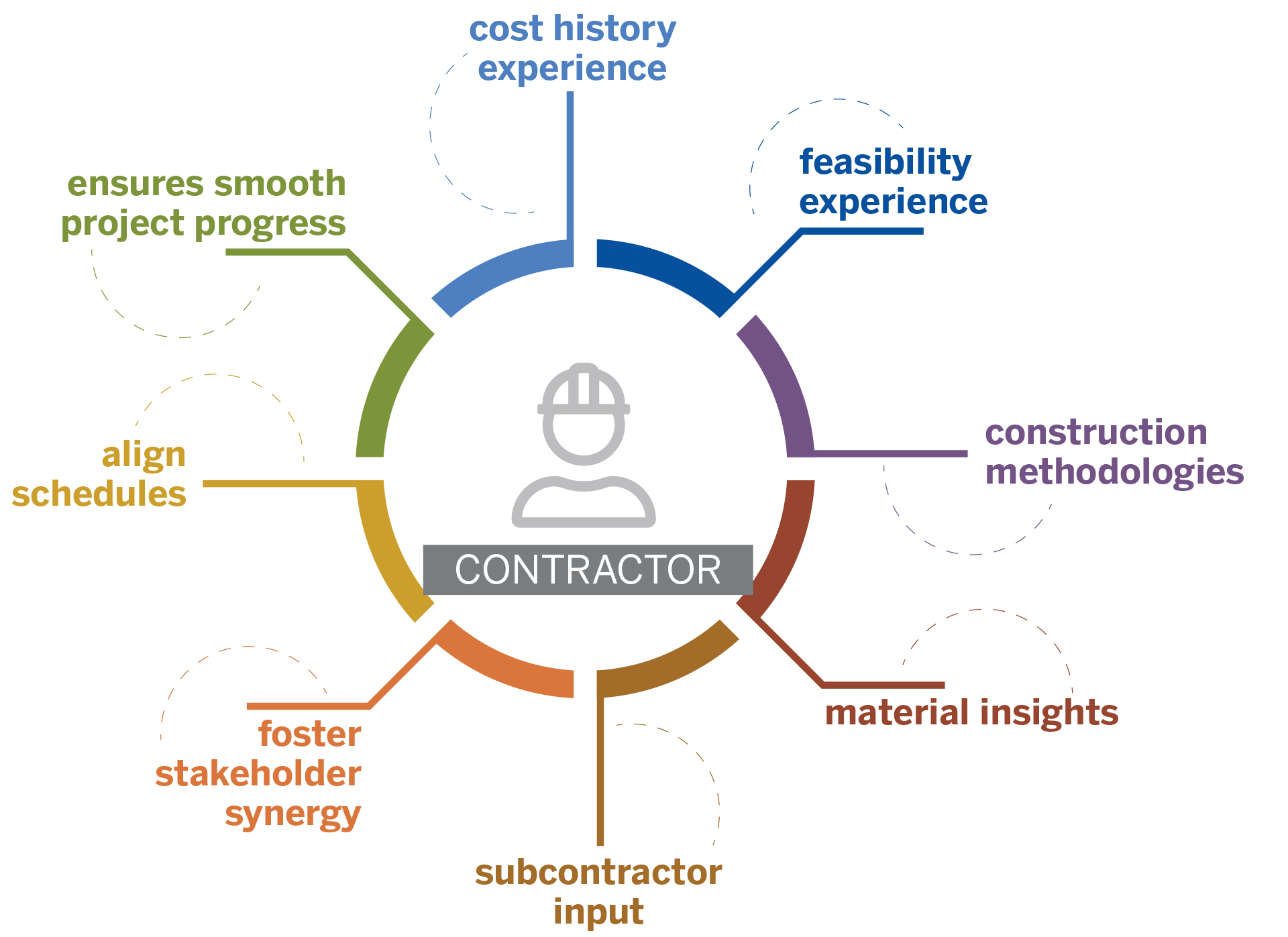
"It’s important for us to have a clearcut sense of purpose behind our work. For example, while we are heavy in Texas construction, we understand that a light touch on the surrounding landscape is just as important as building solid runway infrastructure. We love Texas, we want the landscape to endure, and so our process is efficient as well as caring."
– Kory Keller, owner, Allen Keller Construction
8. Consider environmental impact
It’s important to be mindful of the land, location, and impact your airfield development might have on neighbors and the surrounding environment. Adopt environmentally conscious practices, evaluating site conditions and stormwater and drainage needs to mitigate ecological impact during and after construction.

If your project area needs draining where a wetland may be disrupted or impacted, a delineation will ensure compliance with environmental regulations. Wetland delineations provide precise information about the location of wetlands within the project plan. To obtain a permit for activities that impact wetlands, the delineated wetland boundary must be approved by the U.S. Army Corps of Engineers (USACE) and often requires approval from other local agencies with regulatory authority.
You’ll want to work with your airport engineer or planner to implement a comprehensive plan to ensure compliance and minimize the environmental footprint associated with your runway development. Like most private developments, there are often opportunities to implement eco-friendly materials and practices during the planning and construction of the airfield, such as using recycled or renewable resources, minimizing waste and emissions, and integrating natural elements into the design.
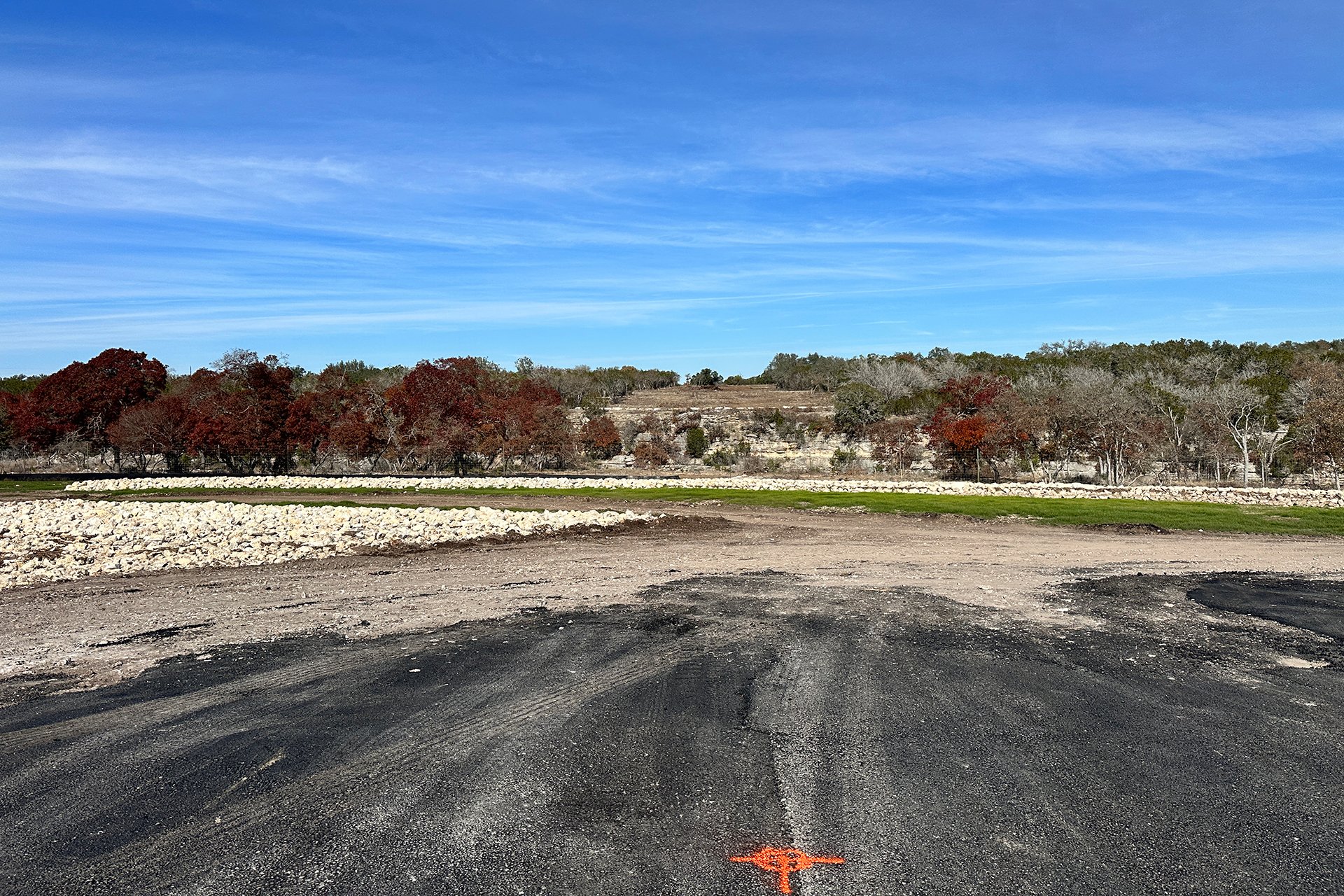
9. Integrate safety measures
It’s important to implement comprehensive safety protocols, including lighting and navigational aids, clear approach and departure paths, and proper grading of the safety areas and runway area. FAA standards are strongly encouraged for private-use airports as they can serve as a guideline for safety and efficiency throughout the development of a private airfield. The FAA’s Advisory Circular (AC) 150/5300-13B, Airport Design, provides safety standards that are implemented at public-use airports around the country and should be implemented on your private airfield.
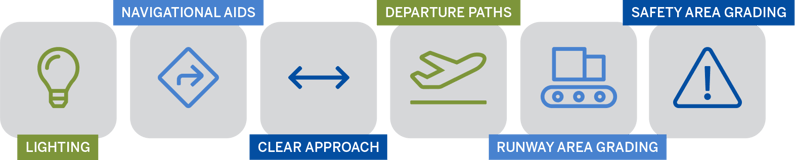
If you are interested in developing instrument flight procedures at your private airport, close collaboration with the FAA’s special instrument approach procedure team or the FAA’s authorized private Coded Instrument Flight Procedures (CIFP) developer will provide additional considerations and a cost estimate for the development and maintenance of the procedure.
10. Consider long-term maintenance
To protect this investment, it’s essential to develop and implement a proactive plan for sustained upkeep and maintenance. This plan involves regular inspections, timely repairs, and facility updates to ensure safety and compliance, as well as extend the lifespan of the private airstrip. By understanding the ground conditions and pavement materials used in construction, we can develop a long-term maintenance plan that includes a preventive maintenance schedule and cost estimates.
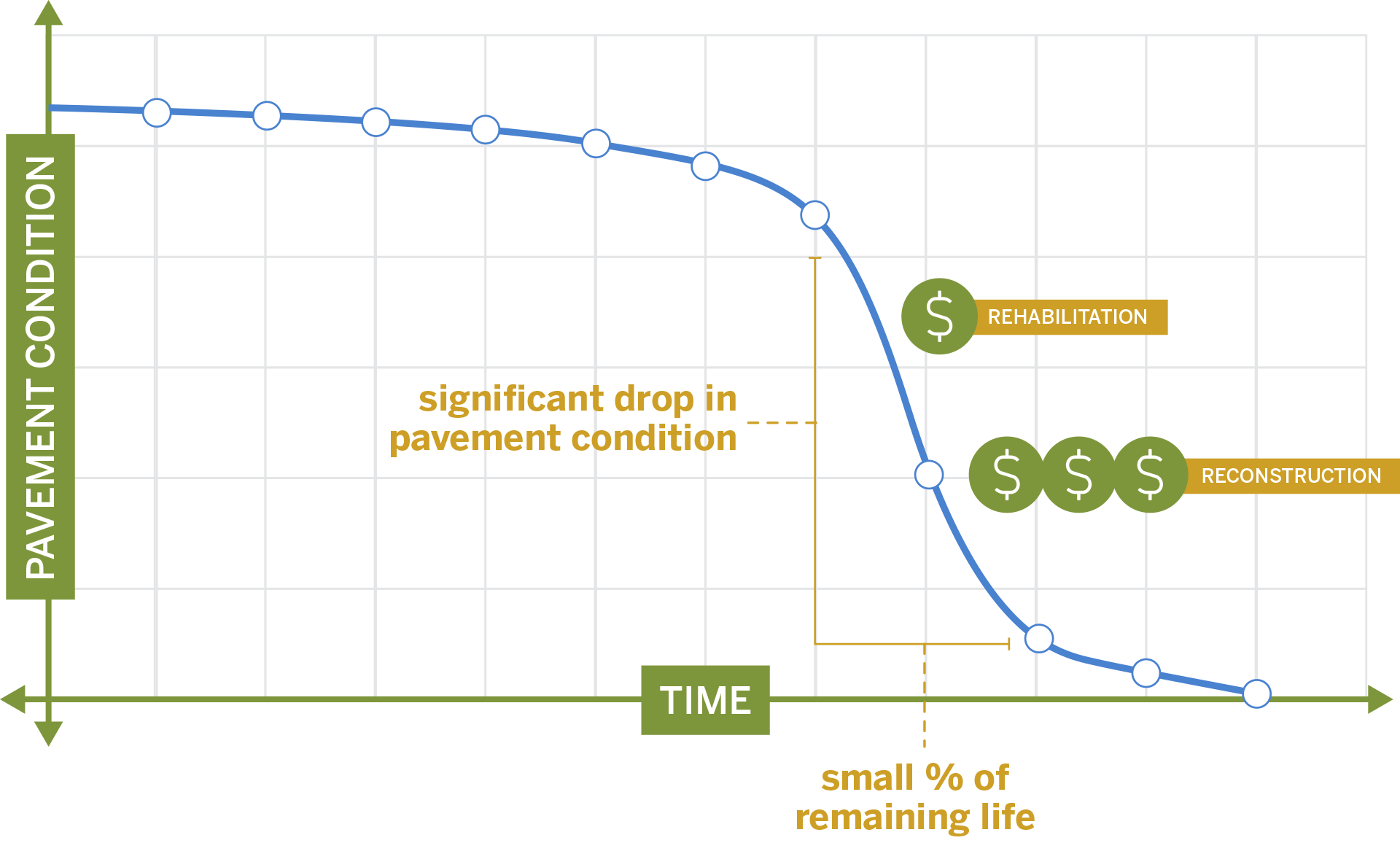
Developing a long-term maintenance plan will extend the useful life of the airstrip, which provides peace of mind and savings in the long run.”
- Jake Jorgenson, airport engineer
Whether you're in the initial planning stages or ready to take proactive measures for your private runway development, our team is ready to help with the next steps.
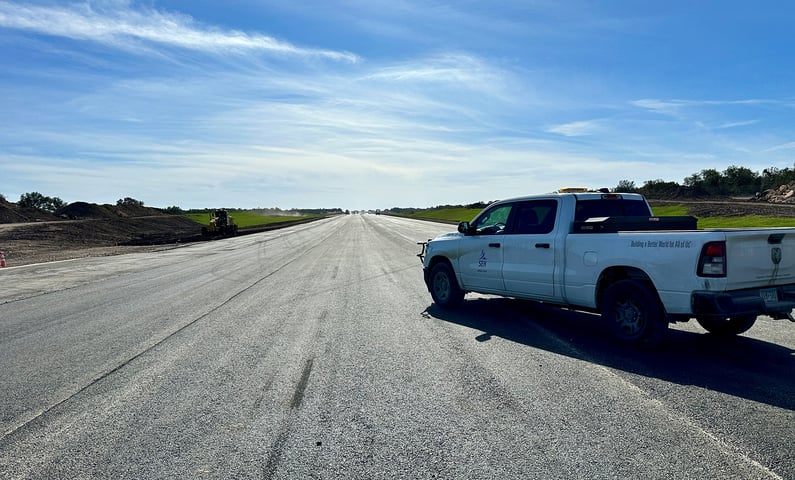
About the Experts
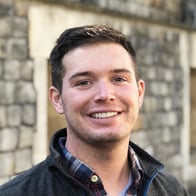
Matt Stewart is an airport planner and project manager with experience in terminal operations, private development, public and non-public areas, airfield operations, as well as airport security and badging. Matt has a vast knowledge of daily airport activities, including evaluating runway safety areas and ensuring FAA compliance.
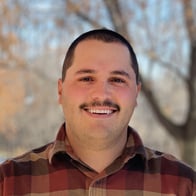
Jake Jorgenson, PE*, is an airport engineer experienced in leading complex design, project cost estimating, pavement design, and construction administration. Jake has worked with private clients and public airports on a variety of runway and taxiway reconstructions, apron and parking lot design and construction, airfield electrical improvements, and new/relocated fuel system projects
*Registered professional engineer in MN, TX
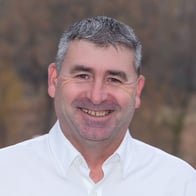
Randy Jenniges, PE*, is a civil engineer, SEH principal, Board of Director, and the company’s director of land development. He specializes in ensuring property projects, ranging from 40 acres to more than 1,000 acres, achieve the best possible return on investment.
*Registered professional engineer in MN, NC, and TX